Stereolithography (SLA) belongs to the VAT polymerisation category of 3D printing that utilizes light curable thermoset resins to build parts. It is a powerful 3D printing technology that produces extremely accurate and high-resolution parts that are capable of being used directly in end-use, low-volume production, or for rapid prototyping.
How does stereolithography work?
An SLA printer consists of four primary sections:
- A tank filled with the liquid resin which is usually a clear and liquid plastic
- A perforated platform is immersed in the resin tank. It can be lowered into the tank and can move up and down along the Z-direction depending on the printing process
- A high-powered, ultraviolet laser
- A computer control unit that controls both the platform and the UV laser movements

After the CAD data is fed into the system, the stereolithography printing process follows the next steps:
- Step 1 – The UV laser draws the first layer of the print into the photosensitive resin. Wherever the laser incidents, the photo liquid solidifies. The laser is directed to the appropriate coordinates according to the design.
- Step 2 – After the first layer, the platform is raised according to the layer thickness (about 0.1 mm) and the additional resin is allowed to flow below the already-printed portion. The laser then solidifies the next and the process is repeated until the whole part is complete. The resin that is not touched by the laser remains and can be reused.
- Step 3 – After finishing the part, the platform rises out of the resin tank and the excess resin is drained. At the end of the process, the model is removed from the platform, washed of excess resin with alcohol and then placed in a UV oven for final curing. Post-print curing enables objects to reach the highest possible strength and become more stable.
- Step 4 – The support structures are removed during the post-processing process.
Materials for SLA 3D Printing
Amongst the most widely used materials for SLA, Xometry offers:
- Rigid plastics: such as ABS SL 7820, PC – Like Heat Resist Translucent, Xtreme Polypropylene…
- Silicone rubbers: such as True Silicone
Advantages of stereolithography
SLA is one of the most reliable and precise 3D printing methods for prototyping and also for industry grade applications with high resolution. It has a set of advantages that makes it unique.
SLA offers fine details and high precision
Layer thickness obtained by stereolithography is very less (0.05 to 0.10 mm) and with the very thin laser beam, it is possible to obtain minute complex features with a very realistic finish. It is also possible to create small parts with high definition, as well as larger parts up to two meters in size, while maintaining high precision and tight tolerances.
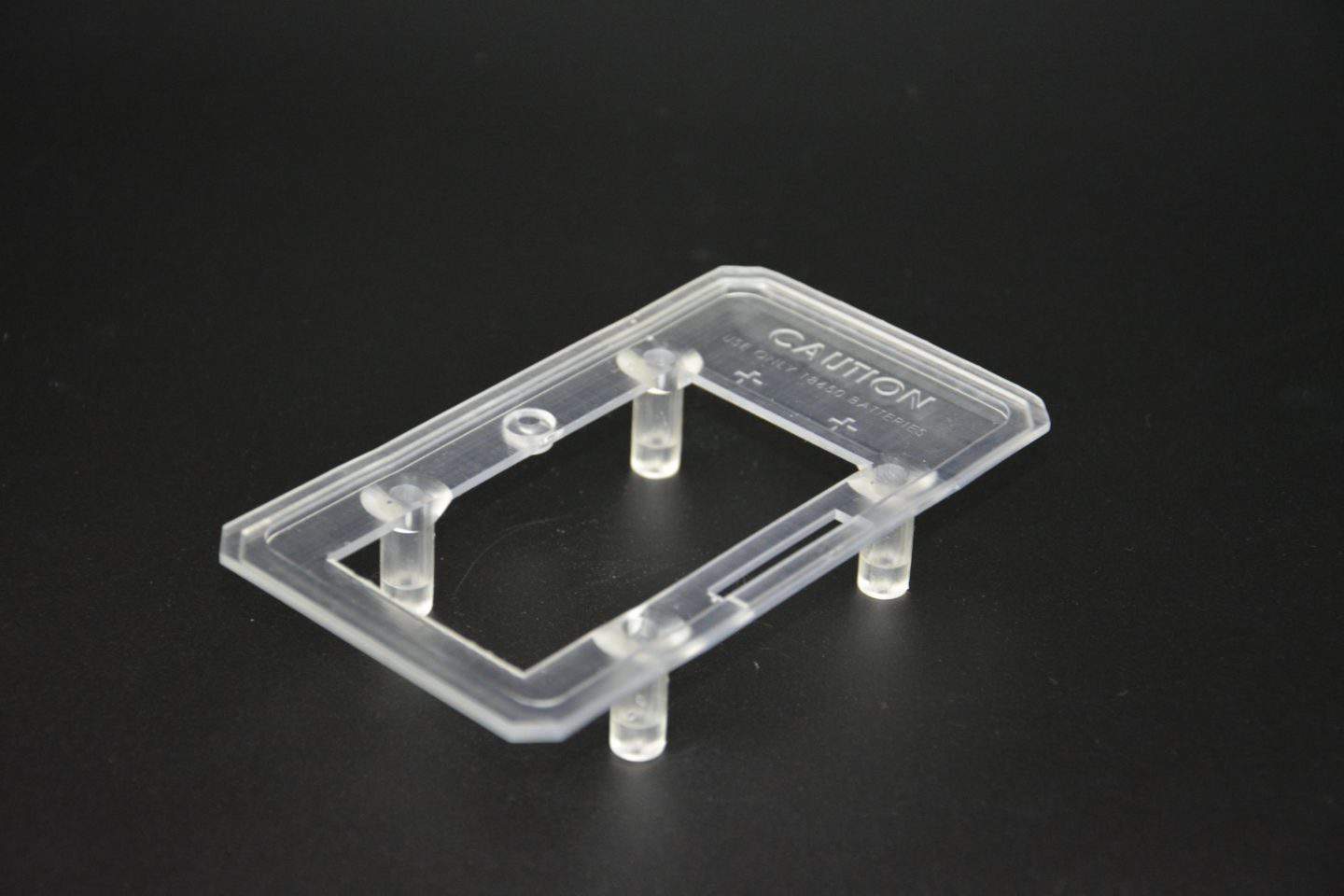
Stereolithography is good for complex designs
Even though SLA utilizes support structures, it is good for complex designs since it uses resins unlike its counterparts like SLS and MJF which uses powders. The resin usage gives fluidity to the design which helps in achieving complex internal features.
SLA parts have a smooth surface finish
Since SLA utilizes resin materials, the surface finish will be glass-like and can replace normal prototypes made from MJF or SLS. Due to its top quality surface finish and high definition, the external as well as internal details can be seen perfectly. It is also good for functional prototypes for a general overview.

No wastage of material with SLA
The thermoset resin that is drained after the part is made can be used again without any wastage. The material waste produced by SLA is negligible and is also a key factor in choosing SLA as a cheaper option for 3D printing projects
SLA parts are food grade and bio compatible
Resins like True Silicone which are used in stereolithography are bio compatible and one of the major advantages of SLA. Other technologies like MJF don’t have the food grade or bio compatible materials to print, making SLA one of the best technologies to print medical implants or food containers.
Limitations of stereolithography
Limited choice of SLA compatible materials to print
SLA printing does not offer a wide selection of materials to print like FDM. Even with resins, it only utilises thermosetting resins which makes the technology very limited with build materials.
Stereolithography is quite expensive
Stereolithography is more expensive compared to its cheaper counterparts like MJF and FDM that also are widely used to build prototypes. This is mostly due to more expensive photochemical processes and materials.
SLA materials have low mechanical properties
Most standard resins are good for delicate, detailed structures, majorly used for exhibition purposes like prototypes. SLA resins are not comparable in strength and mechanical performance to filaments such as PC, nylon, PETG or other tough FDM materials. Hence they are not recommended for intense stress operations or cyclical loads.
SLA has a low volume of production
SLA 3D printing resins typically cost more and produce less parts per unit of resin than FDM 3D printing filament spools or MJF powders. They usually have smaller build volumes when compared to FDM 3D printers and are not advisable for a batch production because of the time and cost compared to its counterparts.
Xometry’s SLA 3D printing services
Xometry Europe offers stereolithography services online, for on-demand 3D printing projects, for both prototypes and large batches. With a network of more than 10,000 partners worldwide, Xometry is able to deliver SLA 3D printing parts in up to 3 days. Upload your CAD files to Xometry Instant Quoting Engine to get an instant quote with various manufacturing options available for SLA 3D printing.
推荐阅读:3D打印加工服务