折弯是一种变形形式,也是钣金加工中的三种主要工艺之一;另两种工艺是切割和连接。折弯的方法是通过使用夹具或模具将工件保持在适当的位置并策略性地在工件的区域上施加力。施加的力必须超过材料的屈服强度,才能导致零件的塑性变形。此过程会在轴上产生v形、u形或槽形,从而创建新的零件几何图形。弯曲会改变形状,但工件的体积保持不变。
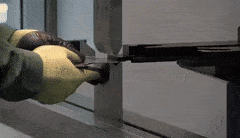
钣金弯曲的类型
金属板材弯曲有多种方法。它们是:
空气弯曲:这使用了两个模具;上模(也称为凸模)和底模。底模具有V形开口。凸模迫使金属薄片进入底模。空气弯曲不像其他方法那样精确。
触底:在这种方法中,通过凸模将金属薄片压到模具的表面上。然后,金属占据最终角度,与模具的角度相同。对于约3毫米厚的板材,v型模开口的最佳宽度是材料厚度的6倍,对于12毫米厚的板材,最佳宽度是材料厚度的12倍。
铸造:这类似于空气弯曲。然而,所使用的力通常是空气弯曲力的5至30倍。这给出了高得多的精度。
折叠:夹梁用于固定金属的较长边。梁可以自由上升,并围绕弯曲轮廓弯曲图纸。负和正弯曲角度都是可能的。
擦除:板材的长边被夹住,工具上下移动,围绕弯曲轮廓弯曲金属。擦拭相对比折叠更快,但具有更高的产生刮痕或损坏纸张的倾向。
旋转弯曲:上模由可自由旋转的圆柱体制成。弯曲的最终形状被切割成它,以及匹配的底模。当辊接触纸张时,其旋转。这一过程使板材弯曲。
啮合弯曲: 偏移弯曲。两个相反的弯曲各小于90度。中性网将相反的弯曲分开。
弯曲的设计心得
为确保无挂钩弯曲并避免变形,以下10个技巧在设计时至关重要。
1. 零件厚度
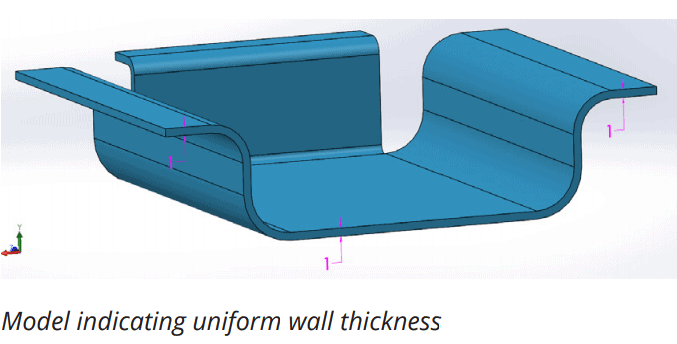
零件必须始终具有均匀的壁厚。Xometry Europe能够制造厚度高达6.35毫米的弯曲钣金零件,但此公差主要取决于几何形状。
2. 孔槽间隙
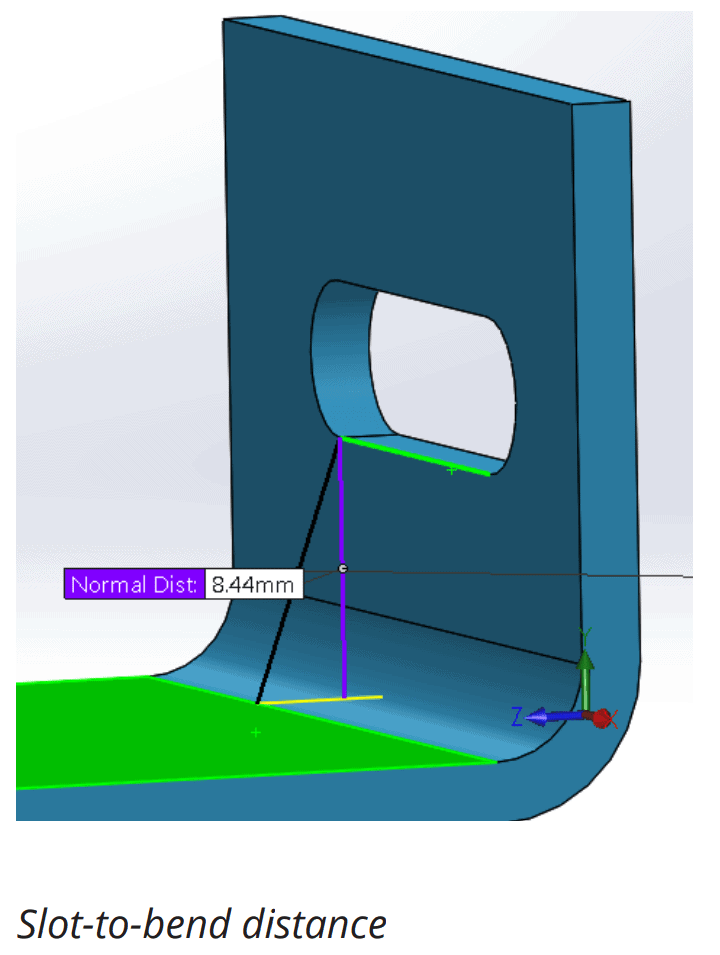
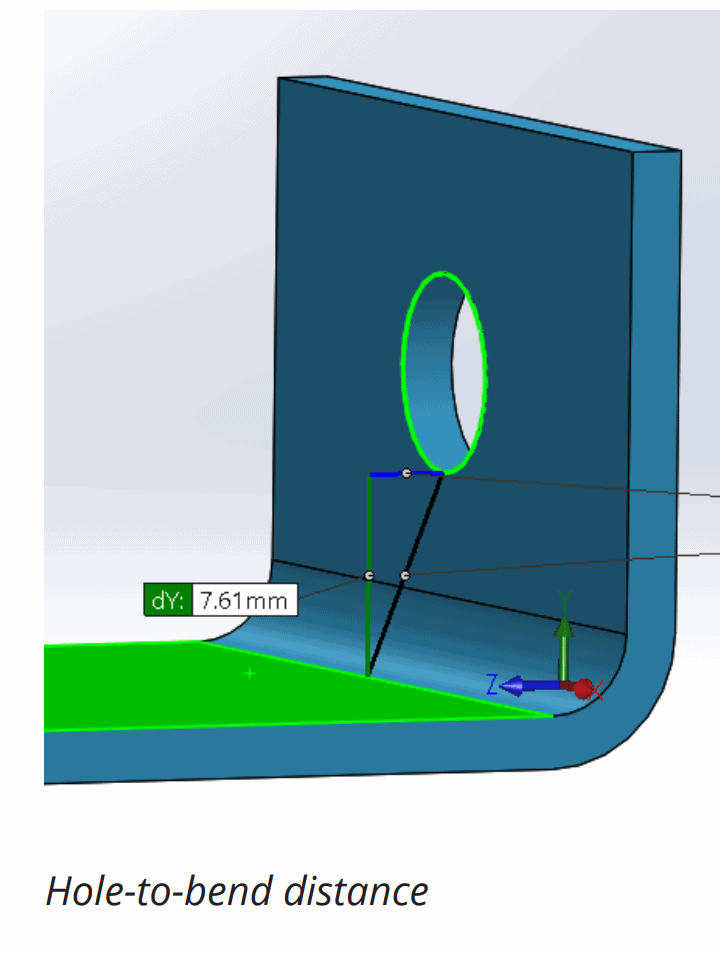
孔距弯曲的距离应至少为材料厚度的2.5倍。槽需要更大的间隙。槽距弯曲边缘的距离应至少为材料厚度的4倍。这是因为孔和槽在靠近弯曲放置时可能会变形。此外,若要避免鼓胀效果,请将这些特征放置在距离零件边至少2倍材料厚度的距离处。
3. 弯曲半径
弯曲半径必须至少为材料厚度的1倍,以防止零件断裂或扭曲。此外,弯曲半径应保持一致,以将成本降至最低。
应在一个方向上设计同一平面中的所有弯曲,以防止零件重新定向。这样既省钱又省时间。
大而厚的零件不应有小的弯曲,因为它们很容易变得不准确。根据经验,内部弯曲半径应至少等于材料厚度。
4. 卷曲
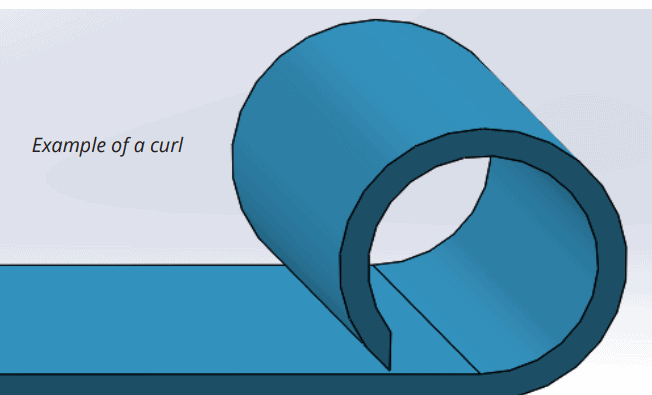
卷曲的外部半径必须至少为材料厚度的两倍。
此外,孔距卷曲的距离应至少等于卷曲半径加上材料厚度。其他弯曲应远离卷曲放置,距离至少为材料厚度加上卷曲半径的6倍。
5. 埋头孔间隙
板金零件上的埋头孔通常用手工工具制造。深度不得超过材料厚度的0.6倍。这意味着10 mm厚材料中埋头孔的最大深度应为6 mm。
此外,埋头孔与弯曲的最小距离必须为材料厚度的3倍,与边缘的最小距离必须为4倍,彼此之间的最小距离必须为8倍。
6. 褶边
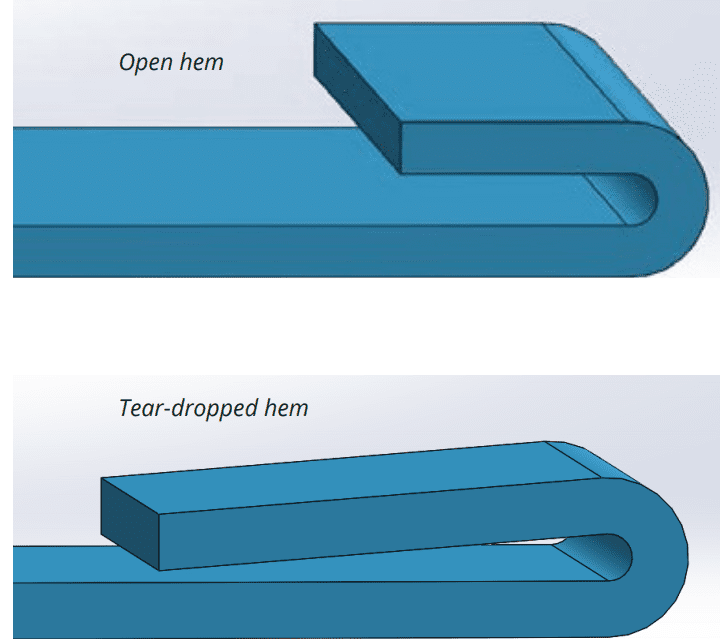
褶边是在零件边缘创建的折叠,用于创建安全的倒圆边缘。有三种不同设计规则的摺边设计。
对于开口褶边,最小内径应至少等于材料厚度,因为较大的直径将导致失去圆形度。为确保完美弯曲,返回长度应为材料厚度的4倍。
泪珠褶边的最小内径也应等于材料厚度。开口应至少为材料厚度的¼,而运行长度应至少为半径后材料厚度的4倍。
7. 斜切边
法兰上的斜面必须为弯曲留出足够的空间,以避免零件变形
8. 连续弯曲
除非绝对必要,否则应避免连续弯曲。连续弯曲的常见问题是难以将已经弯曲的部分装配在模具上。然而,在不可避免的情况下,中间部分应长于法兰。
9. 缺口和凸舌间隙
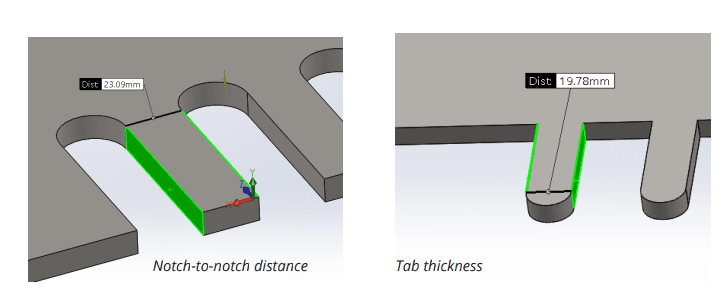
缺口至弯曲距离应至少为材料厚度加上弯曲半径的3倍。另一方面,接片必须彼此相距1 mm或材料厚度,取最大值。
10. 减压切口
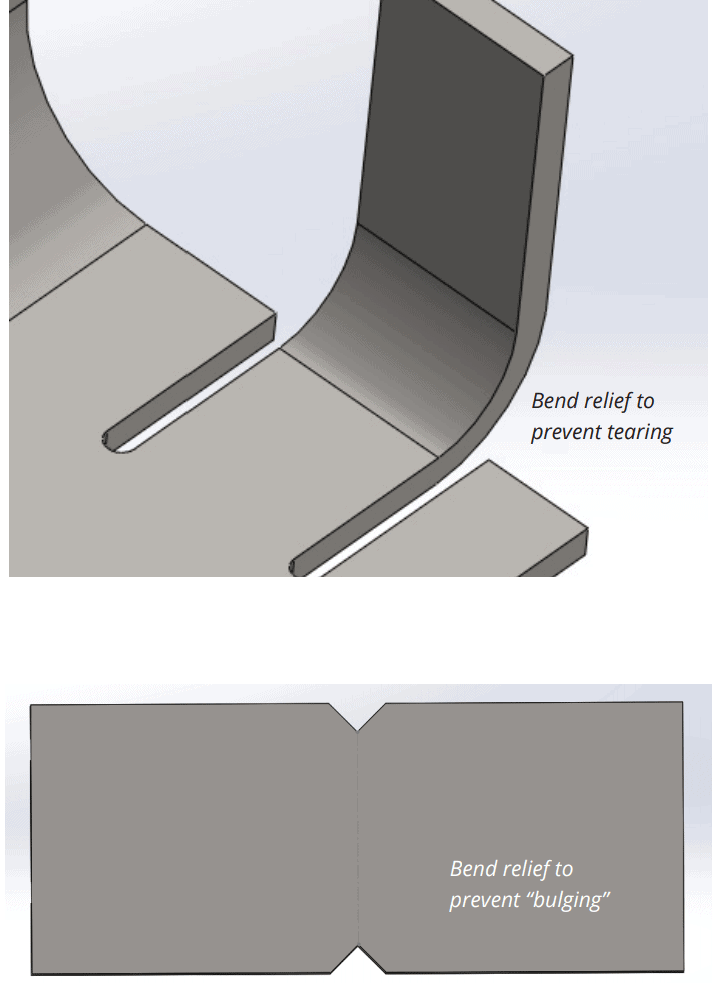
在避免弯曲处出现鼓胀和撕裂时,减压切口至关重要。释放切口的宽度应至少等于材料厚度,长度应长于弯曲的半径。
计算所需弯曲力
在工件中创建正确的弯曲涉及不同的因素。其中包括:
- 材料的弯曲强度
- 弯曲度
- 工件厚度
- 弯曲角度
- 内部半径
- V形模具开口
- 最小内部边缘
下表可用于计算以90°角弯曲不同厚度、不同形状的软钢S235所需的弯曲力。软钢S235的弯曲强度为42 kg/mm²。可变参数如下。
- S (mm) – 工件厚度
- V (mm) – V形模具开口
- B (mm) – 最小内部边缘
- Ri (mm) – 内部半径
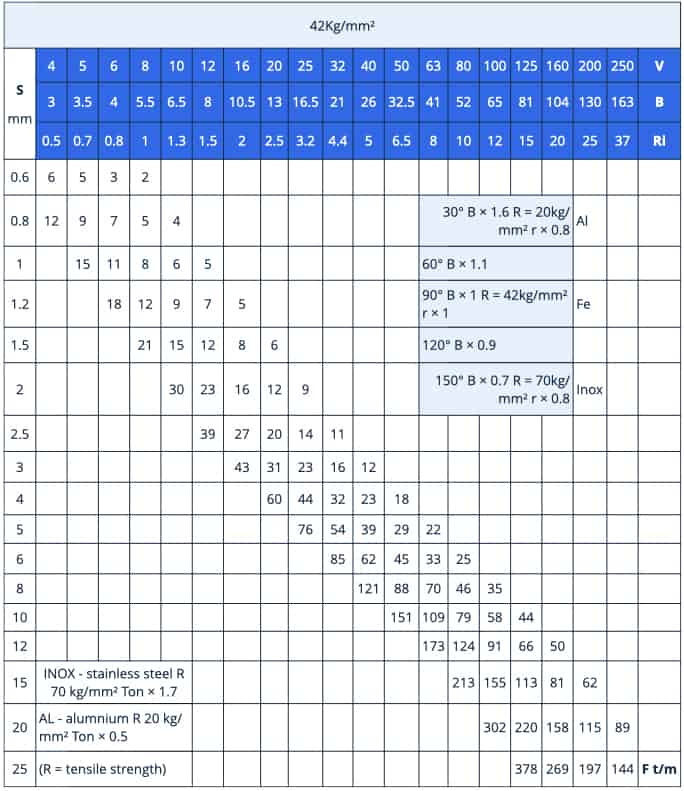
结论
在Xometry Europe,我们提供高精度、快速和高质量的钣金弯曲和制造服务,用于由铝、钢、铜合金等钣金制造零件。使用自动弯曲技术,我们保证高精度和现成零件的质量。
我们也可以根据您的要求进行后处理。要获得即时报价,请在我们的即时报价平台上传您的模型。
推荐阅读:精密钣金加工制造