Computer Numerically Controlled (CNC) machining is a swift, efficient, accurate, and versatile process. This manufacturing method is compatible with a wide range of hard and soft engineering materials, including metals, plastics, semiconductors, elastomers. It is both used in prototyping and for the production of fully functional end-use products. The success of a CNC machining project and the functionality of the produced part depend significantly on the material used. This is why material selection is an essential step in CNC manufacturing that has to be done carefully.
Several factors and requirements determine the suitable material for a CNC machining project. For example, do you need a material with excellent mechanical properties? On the other hand, is high production speed the priority? Quite often, a consideration of numerous factors determine the suitability of a material. The following factors are not exhaustive but will establish a firm foundation when selecting materials for CNC machining.
Materials selection process
To succeed in choosing the best possible material for CNC machining, you can follow these basic steps:
- Step 1 – Determine material requirements. Consider the properties such as functionality, electrical properties, strength and hardness the material should possess to be the most suitable candidate for your project. Also, take into account the operating environment the part will be used in and the conditions it will be exposed to.
- Step 2 – Identify potential material options. Sort out all the suitable materials according to your requirements, including the specifications of your design.
- Step 3 – Select the most appropriate material. Choose the material which fulfils the largest number of your requirements. Sometimes a compromise needs to be made, for instance, a material with good machinability over a more low-cost one to ensure the quality of the part.
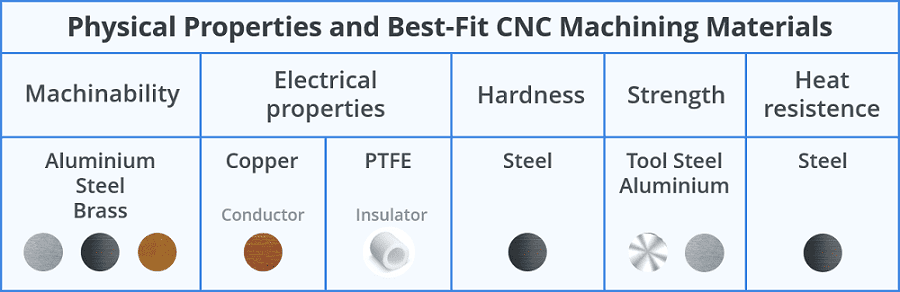
CNC machining materials selection guidelines
Here are the most important factors to take into account when selecting the right material for CNC machining projects.
Part Application
This is one of the most essential and foremost considerations in selecting material for CNC manufacturing. Different applications require different materials. A part produced for aerospace application has to be lightweight compared to a part for building structural support. For example, aluminium 3.3211 is commonly used in the aerospace industry for its good strength to weight ratio.
The application area will determine the material’s physical properties such as tensile strength, strength to weight ratio, crack resistance, rigidity or flexibility. Generally, heavier materials withstand more stress, but in weight-sensitive applications, then lighter materials with good strength to weight ratios must be selected. Steel 1.0503 and 1.0038 are relatively heavy materials, compared to lighter aluminium alloys such as aluminium 3.3206.
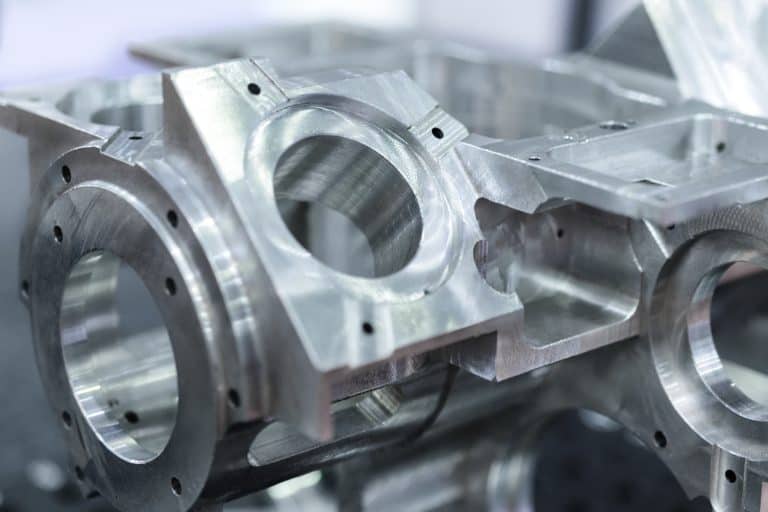
Operating Environment
The environment in which the part will be used is a critical factor in deciding the material. Operating conditions include temperature, harsh chemicals, exposure to UV radiation, continuous contact with water and even subjection to flames. Any material selected must have its melting temperature safely above the operating temperature. If this is not the case, the part might undergo structural variations when exposed to the high operating temperature.
In addition, the part selected must be able to withstand the heat that comes from the machining operations. Steel 1.4404 has great heat resistance, up to 861°C. It is easy to predict the temperature or moisture conditions a material will be exposed to in indoor usage to a certain degree of accuracy. With this, choosing a material becomes more effortless.
However, in outdoor applications, it is best to select materials such as stainless steels that can withstand large moisture concentrations and rusting while maintaining their physical appearance and structure. In addition, extreme weather variations are more likely to occur outdoors; this could cause structural warping in certain materials.
Dimensional Stability and Tolerance
Industries like aeronautics and aerospace require components with extremely precise dimensions and excellent stability. Such conditions will require materials with good dimensional stability i.e. low deformation factor. Different materials respond to the forces generated by the cutting tool in different ways. Therefore, the part selected must be able to attain the tight tolerances required. The more machinable a material is, the easier it is to achieve tighter tolerances.
For example, the high machinability of aluminium makes it possible to produce parts with very high tolerances using this material. Note that tighter tolerances are more expensive to produce. So whenever dimensional tolerance is not a vital requirement, it is advisable to use less tight tolerances to reduce the time and expenses involved in machining the part.
Electrical Conductivity
Certain materials, such as copper and silver, are excellent conductors. On the other hand, PTFE is a good insulator. For parts for electrical applications, the choice of material will depend on the electrical properties required of the part. Therefore, it is vital to consider the electrical conductivity of the chosen material. Metals are generally good conductors of electricity, while plastics are typically good insulators.
Machinability
If a part needs to be produced in large quantities or batches, it is more suitable to choose materials with easy machinability to reduce time and expenses. Materials like aluminium, brass are much more machinable than tool steel, even though the latter has more strength. Materials with low machinability should only be chosen if they are to be produced in smaller numbers and product turnover time is flexible enough. Such materials require more resources, time, and effort to machine.
Note that machinability is a secondary consideration during material selection and should not be considered at the expense of other core considerations such as part application.
Physical Appearance
Aesthetics is not usually among the primary considerations when selecting a material. However, in some cases, it is of high importance. For certain products, the physical appearance will determine the general acceptability of such products by the consumers. Consumer products may require specific physical features such as colour or a smooth surface finish.
Metals typically have a good surface finish after machining, thus requiring less work during polishing. Plastics are usually available in different colours, while metals require post-processing to colour them.
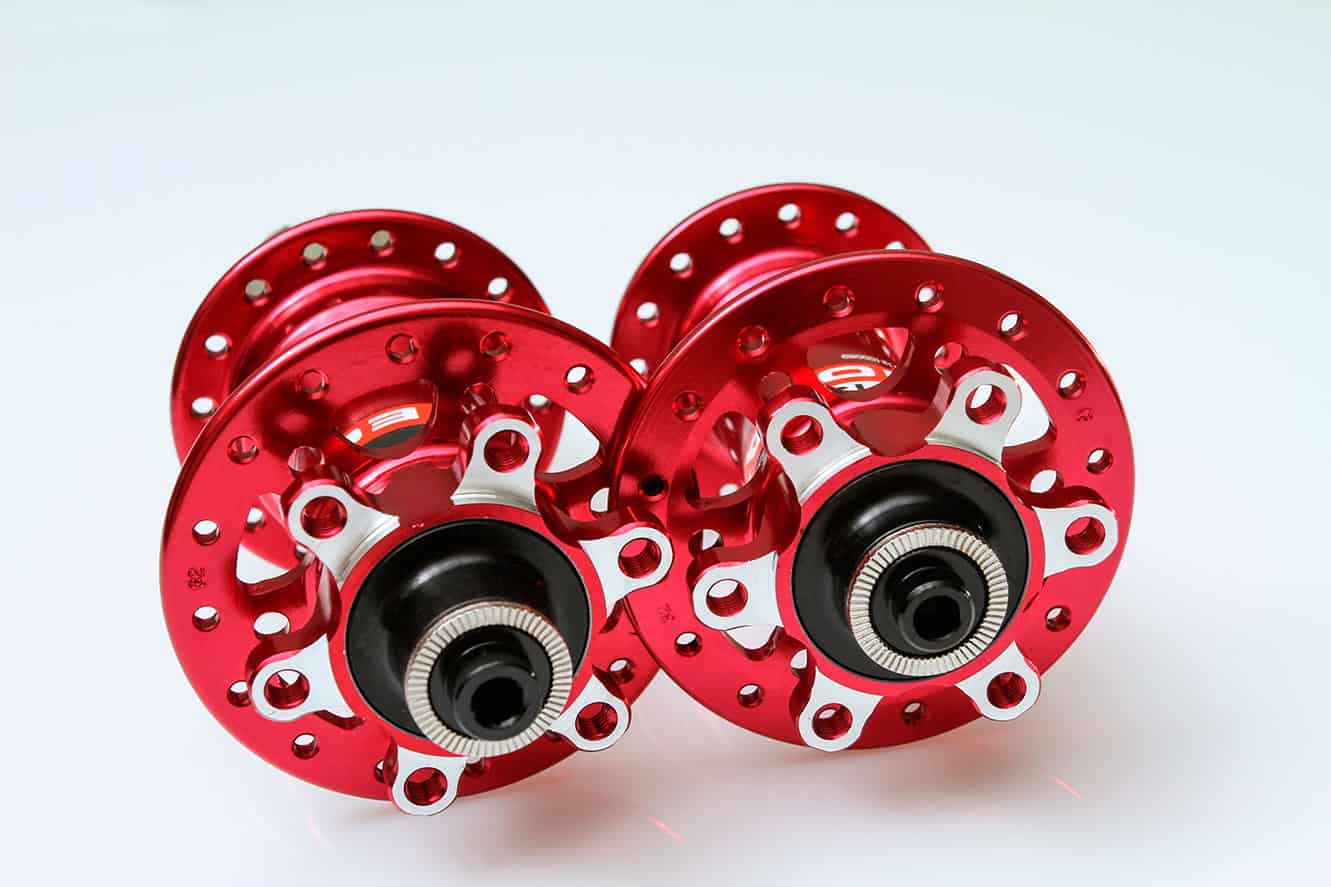
Material Costs
Sometimes, the most suitable material for a part is expensive. The price of acquiring such material stretches far beyond the production budget. It becomes necessary to look at other low-cost materials. However, careful consideration must be given to the functionality, strength, hardness, chemical tolerance, electrical properties, and other properties to determine that such a material is a viable low-cost alternative to the best suitable material. For example, steel 1.4571 has excellent wear and corrosion resistance, as well as good machinability.
However, it is twice as expensive as steel 1.7131 which also has great wear resistance. For applications in which resistance to wear is of the primary concern, steel 1.7131 is a great alternative to steel 1.4571.
Availability
Availability is an important consideration when selecting materials for CNC machining. Sometimes, the most suitable material may not be available in quantities large enough to sustain production. On the other hand, the procurement of such material could be difficult. It is wise to select materials that fit into the functional requirements and are readily available for use, especially if the part will be produced in large numbers. Easily accessible materials ensure that the CNC machining is done in the least possible time and efficiently.
Conclusion
The choice of material influences almost every stage of the product life cycle, from prototyping to full production to the part’s performance in its end application. The key to having a fully optimized finished part begins with selecting the right material.
Therefore, material selection is a vital part that needs to be diligently considered before beginning CNC machining operations. With the above considerations, it becomes easy to narrow down the list of materials that are best suited for the part and make a well-informed choice of material.
推荐阅读:CNC加工技术