Carbon DLS (Digital light synthesis) belongs to the VAT polymerisation category of 3D printing. It uses digital light projection, oxygen-permeable optics, and programmable liquid resins to create products with end-use durability, resolution, and surface finish.
This technology, along with Carbon’s exclusive CLIP resins (Continuous liquid interface production), paves way for product designs previously impossible and complex, including mass customization and on-demand inventory. The Carbon DLS technology enables companies to bring innovative products to market that were never thought possible.
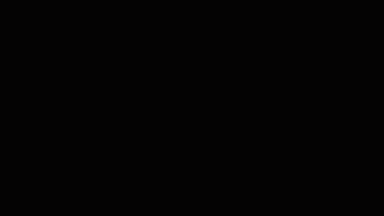
How does Carbon DLS work?
Carbon DLS process involves a liquid plastic resin being cured into solid with the help of a projected UV laser. The laser (5) is projected from below through an oxygen-permeable window (3) and into the reservoir of the resin. The layer sequence of the UV images are projected on the resin (2) and the part solidifies accordingly while the build platform (1) rises. This process is called Continuous liquid interface production (CLIP).
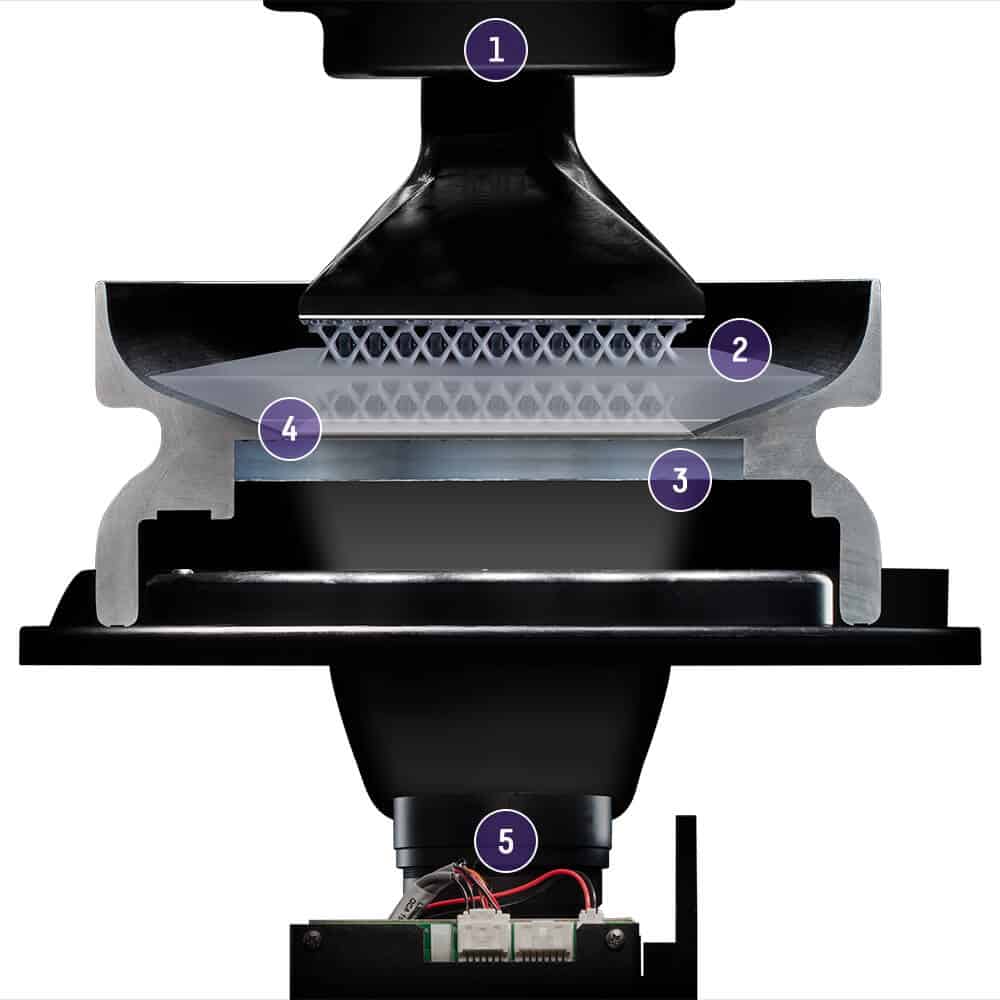
- Step 1 – A thin liquid layer of uncured resin is placed between the oxygen permeable window and the printing part is called the ‘dead zone’ (4).
- Step 2 – The light that passes through the dead zone, cures the resin above it without curing the part onto the window. This continuous flow of uncured resin below the cured resin goes on as the print progresses and hence the name, continuous liquid interface.
- Step 3 – After the part is printed, it is baked in an oven. Heating induces a chemical reaction in the resin that improves the mechanical properties of the part.
This very uninterrupted process (step 2) is what distinguishes Carbon DLS from other Vat polymerisation technologies.
Materials for Carbon DLS 3D printing
Amongst the most widely used materials for Carbon DLS, Xometry offers:
- Rigid plastics: such as CE 221, UMA 90, DPR 10, EPX 82, FPU 50, RPU 70
- Rubber-like plastics: such as EPU 40, SIL 30
Advantages of Carbon DLS technology
When coming to Carbon DLS, these are the most important factors that make it standalone.
Complex designs are easy to achieve
Although Carbon DLS technology produces support structures, it is good for complex designs since it uses resins unlike its counterparts of Powder bed fusion like SLS and MJF. The resin usage gives fluidity to the design which helps in achieving complex designs and complex internal features. Most of the complex designs that cannot be achieved even with conventional machining like CNC, are possible with Carbon DLS.
Indeed, this 3D printing technology allows to create undercuts and perfectly straight walls without sacrificing manufacturability. Plus, the production of lattice structures, which is unique to Carbon DLS, empowers engineers to redesign products (for instance, lattice design can replace foam in shoes).
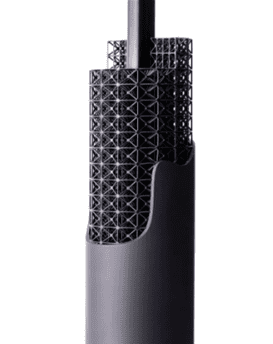
Good mechanical properties
What differentiates Carbon 3D prints from the ones printed with similar processes like Stereolithography (SLA) or PolyJet is that the resin has a secondary thermal step which activates dormant epoxies or urethanes, making parts much stronger than UV-curing alone. Additionally, the DLS process is continuous, without stopping layer-by-layer as with most additive manufacturing. This gives the parts isotropic properties, meaning that strength is consistent, regardless of orientation. This is a significant advantage over processes like Fused Deposition Modeling (FDM), where Z-direction features can be much weaker than similar features built in the XY-direction.
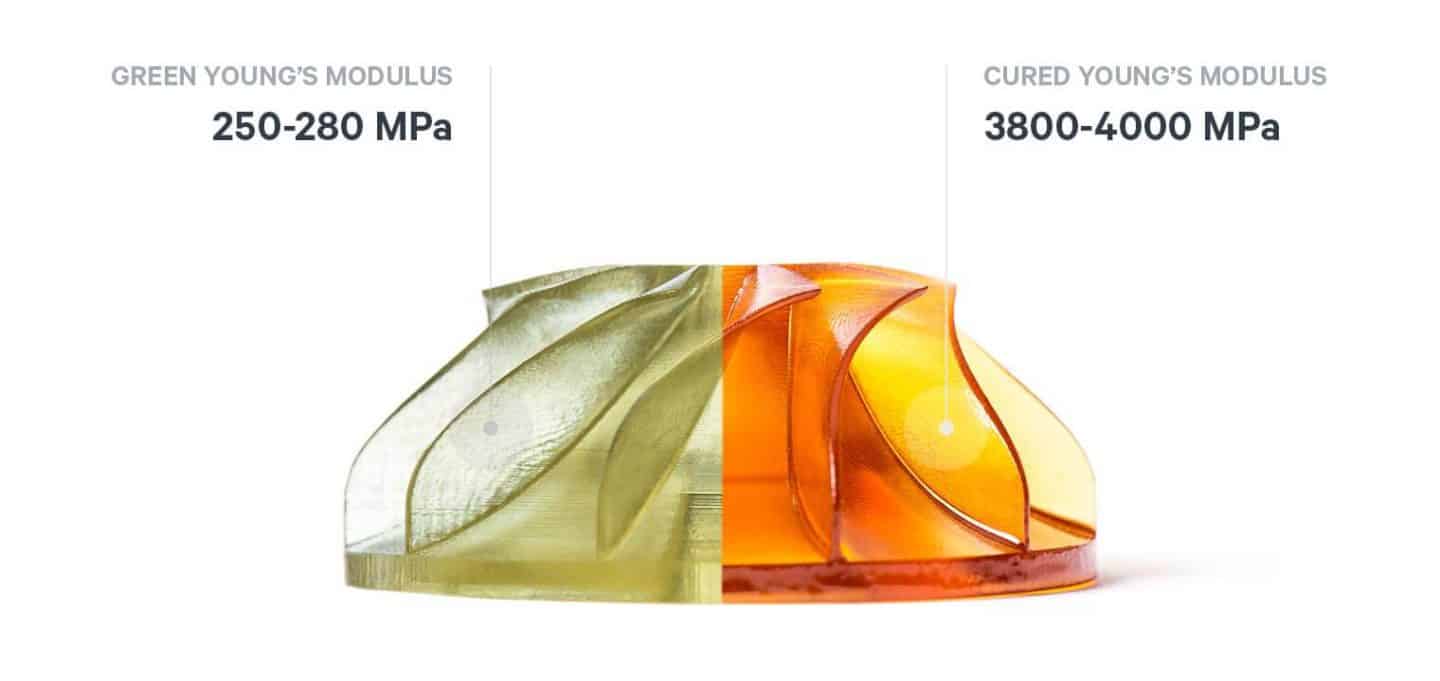
Smooth surface finish
Since Carbon DLS utilizes resin materials, the surface finish will be glass-like and can replace normal prototypes made from MJF or SLS that use powder or FDM that uses filaments. Due to its top quality surface finish and high definition, the external as well as internal details can be produced perfectly. It is also good for functional prototypes for a general overview.
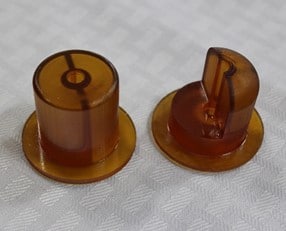
Finer details and high precision
Layer thickness obtained by Carbon DLS is very less (0.001mm) and with the very thin laser beam, it is possible to obtain minute complex features with a very realistic finish. This 3D printing technology also allows the creation of small parts with high definition, as well as larger parts up to two meters in size, while maintaining high precision and tight tolerances.
No wastage of material
The CLIP resin that is drained after the part is made can be used again without any wastage. Compared to the waste produced by MJF or SLS, the material waste produced by Carbon DLS is negligible and also a key factor when choosing the right 3D printing technology.
Food grade and bio compatible prints
Resins like SIL 30, RPU 70 which are used in Carbon DLS are bio compatible and are one of the major advantages of Carbon DLS. Other technologies like MJF don’t have the food grade or biocompatible materials to print, making Carbon DLS one of the best technologies to print medical implants or food containers.
Flexible 3D printing options available
CLIP resins like SIL 30, EPU 40, FPU 50 are flexible resins and give the part rubber-like flexible features. They are fit to be even used as functional parts in real time operations.
Considerations about Carbon DLS
Expensive
Carbon DLS is one of the most expensive 3D printing technologies in the market. Compared to MJF or FDM, which are suitable and cheaper for prototyping, DLS technology can become an expensive affair in case of trials and numerous design corrections for prototypes. Single, one-off prototypes are also more costly due to production setup cost factors.
Limited selection of material
Carbon DLS utilises the print material that is quite unique. As of now it has only eight available materials. In addition, only a few colours are possible. However, post processing helps in imparting colour to the part but makes it ultimately a costly affair.
Xometry’s Carbon DLS 3D printing services
Xometry Europe offers Carbon DLS service online, for on-demand 3D printing projects. With a network of more than 10,000 partners worldwide, Xometry is able to deliver Carbon DLS 3D printing parts in up to 5 days. Upload your CAD files to Xometry Instant Quoting Engine to get an instant quote with various manufacturing options available for Carbon DLS 3D printing.
推荐阅读:3D打印加工服务