Injection moulding, a modernised and far more advanced form of casting, is one of the manufacturing methods developed through the years that allows to speed up and enhance the production of different products. Speed and ease of production are critical considerations in manufacturing, especially bulk production, as these bring about numerous advantages. These advantages include lower development costs, greater forecasting accuracy, faster innovation, and larger market share.
What is injection moulding?
Injection moulding is a manufacturing process in which molten material is injected into an already prepared mould and left to cool. Upon cooling, the material solidifies and takes the shape of the mould, before being ejected. While this process may be used for one-off productions, it is usually used in the mass production of identical parts. Materials most commonly used in injection moulding are plastics or elastomers.
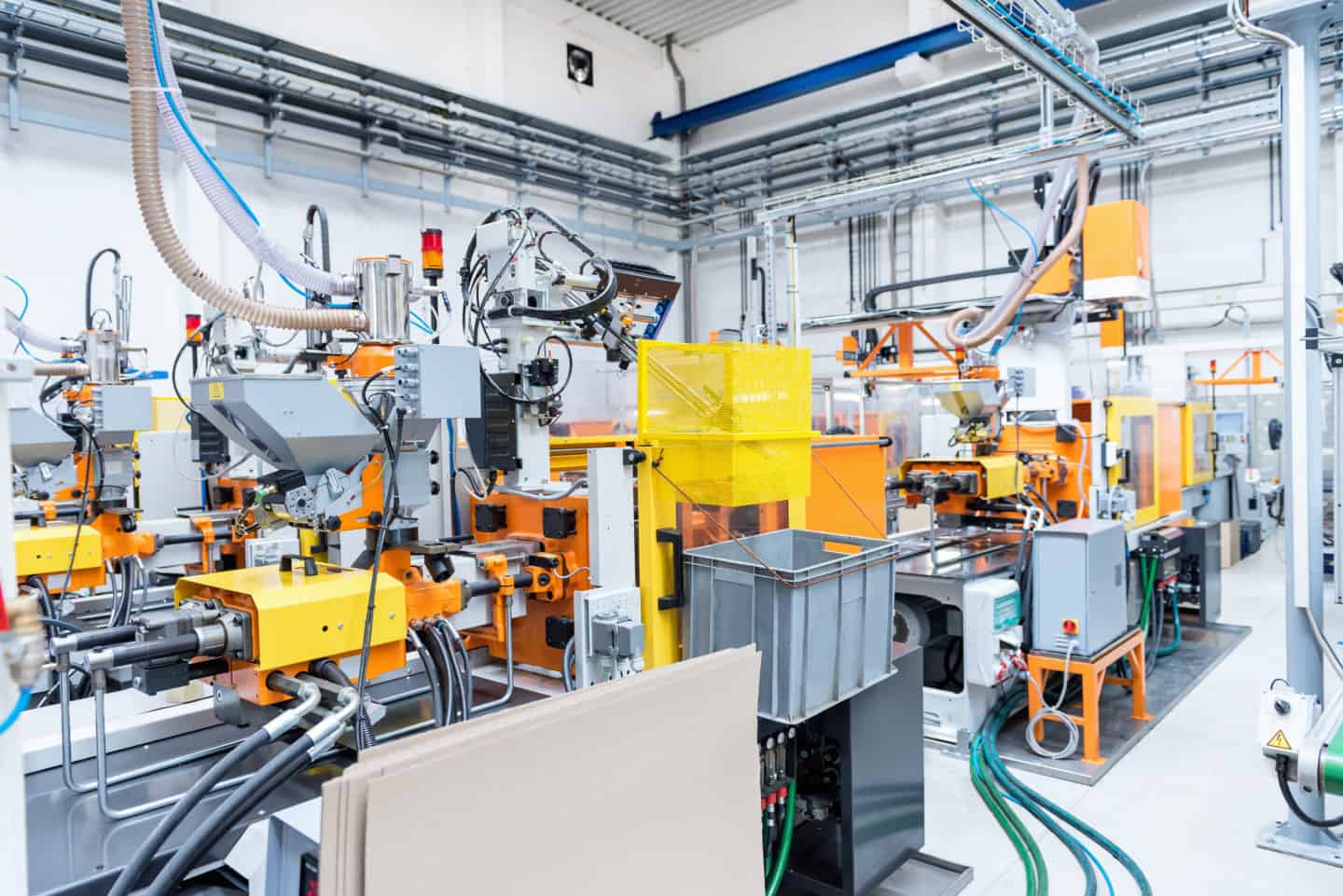
Due to its high output rate and consistency of quality, injection moulding is widely used across different industries to create parts such as electrical components, automotive parts, basic consumer plastics, furniture parts, and many others.
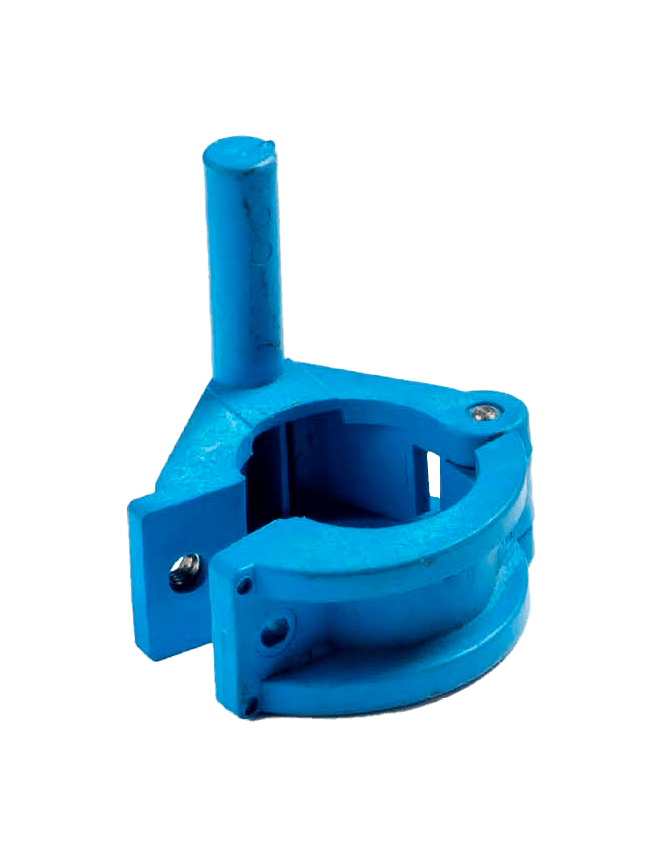
How does injection moulding work?
A special-purpose injection moulding machine carries out injection moulding. The manufacturing process is divided into the various steps listed below:
Step 1 – Creation of the mould
The first step in injection moulding is mould creation. The mould for the part to be manufactured is designed according to the specifications of the part’s 3D model, using computer-aided design, following several injection moulding guidelines. It is then manufactured in two parts, usually using CNC machining. Moulds are made from metals (mainly steel or aluminium).
Step 2 – Injection
The separate halves of the mould are placed in and held together tightly by the clamping unit of the injection moulding machine. In the form of granules or pellets, the raw material is introduced into a barrel where it is heated at a high temperature and pressure till it melts. Now in molten form, the material is immediately injected into the mould cavity, filling the entire space in the mould. It then cools down and solidifies, forming the shape of the mould.
Step 3 – Ejection and finishing
After the material has completely cooled and solidified, the mould is opened by the clamping unit and the solidified finished part is ejected. The finished part is subjected to some post-processing operations. These operations include removing excessive material and support structure, surface finishing, and, if required, painting, electroplating, heat treatment, etc.

Other injection moulding processes
There are other forms of injection moulding that vary from the process described.
Over moulding
Over moulding is an injection moulding process that allows a part to be created from two different materials. The first material is moulded and, before cooling down, the overmoulding material is introduced, creating strong bonds between the substrate and the overmoulding material. This technique is used to create multi-material objects with improved aesthetics and functionality, while eliminating the need for secondary operations.
Insert moulding
Insert moulding is similar to over moulding. In this injection moulding technique a preformed object is inserted into the mould before the molten material is poured. With the point being to have the preformed material inserted into the moulded object. An application of insert moulding is inserting metal screw holes into plastic parts.
Metal injection moulding
In this process, finely powdered metal is combined with wax, polypropylene binders, or other polymers to form a feedstock mix. It is then injected into the mould and left to cool. Once it solidifies, a portion of the blinder is removed using methods such as the catalytic process and the use of solvents.
Die casting
The die casting process, also known as high-pressure die casting, is the forcing of molten metal under high pressure into a mould cavity. The process is as follows:
- First is the preparation of the dies (moulds), which entails the lubricating of the mould cavity to facilitate the easy removal of the casting and to control the temperature.
- After that, the cast is closed and injected with molten metals under relatively high pressure between 1500psi and 25400psi.
Die casting products are made from nonferrous metals such as copper, zinc, aluminium, and lead.
Thin-wall injection
This injection moulding process is used to create plastic parts with very thin walls such as food packaging, parts of equipment, and lab apparatus. The sizes of these parts are larger than their thickness. This process of creating thin walls is more difficult than other processes.
Micro injection moulding
Just as the name implies, “micro injection moulding” is a moulding process used to produce tiny plastic parts with weights of about 1 to 0.1 grams. This facilitates the manufacture of micro parts of various complicated geometries with maximum precision and accuracy.
Gas-assisted injection moulding
In the production of thick plastic parts with injection moulding, there’s the risk of distorted parts caused during the cooling process of the molten plastic. This is prevented from happening in gas-assisted injection. As the molten plastics solidifies, gas is introduced into the mould by gas channels, producing smooth surfaces.
Benefits of injection moulding
Injection moulding, as a manufacturing process, has numerous benefits. Some of these are as follows:
High production output
This is one of the process’ most important advantages. The process takes 20-120 secs to complete a cycle, enabling it to create hundreds of parts per hour.
Minimal cost of labour
The injection moulding process is fully automated and can be operated solely by one operator. Therefore, the production cost is cut due to the reduced number of heads.
Design flexibility
Injection moulding enables manufacturers to create various designs regardless of their complexity and intricacy.
Quality consistency
This process follows a sequential pattern in the creation of identical parts. Therefore the quality of the first would be similar to that of the second, third, and the next.

Low wastage
Unlike other production processes such as CNC machining cuts away substantial parts, injection moulding produces very little scrap. The little unused materials can be gathered and recycled.
Compatibility of multiple materials
With this process, you can use multiple materials and colours simultaneously. And as the ejected part has a finished appearance, there is little or no work to be done after that.
Limitations of injection moulding
Despite its multiple advantages, injection moulding also has some of the following downsides.
Visual defects on the parts
Though the process is precise, minor defects from the injection moulding process may exist in the finished products. Take note that the defects are not such that would affect the workability of the parts. Some defects are warping, jetting, sink marks, flow lines, weld lines, short shots, and vacuum shots.
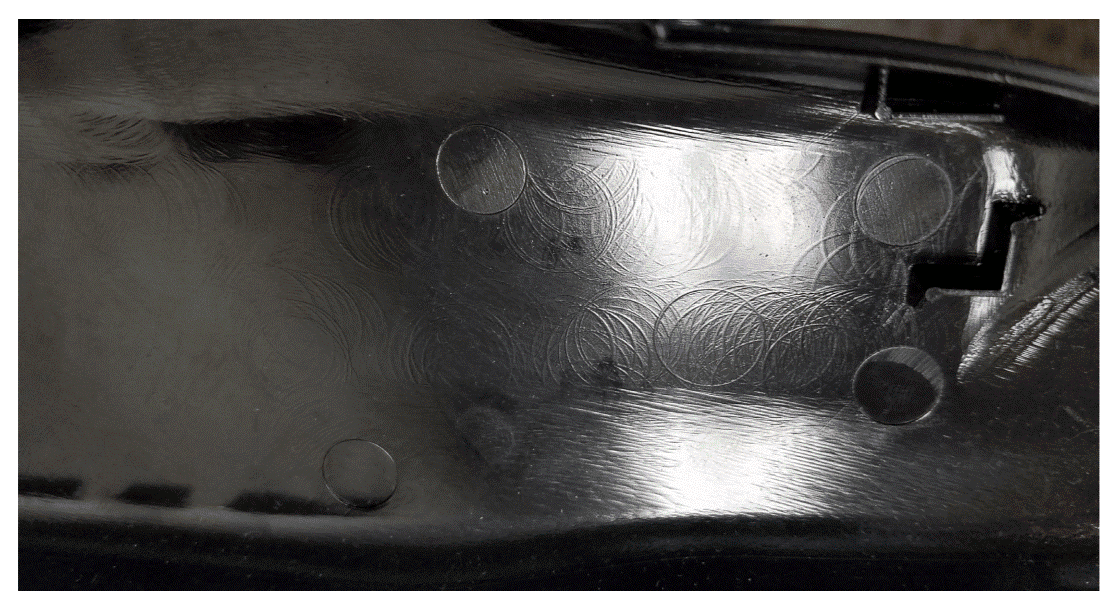
High cost
The setup costs of injection moulding are high. The machines and tools used are expensive. A prototype of the mould also needs to be created and tested. Plus, it takes very skilled workers to design the mould, to avoid future expenses in the part production.
Not suitable for large-sized parts
The production of large parts of equal density is very difficult. This is because of the limitations of the mould. Large parts would have to be created as smaller parts and then combined.
Conclusion
The use of injection moulding in various industries has brought about the seamless and precise production of parts in mass within a short period. Through our extensive network of manufacturers, Xometry Europe offers injection moulding services for several dozens of materials including plastics and elastomers. Simply head over to our Instant Quoting Engine to upload your model and receive a quote to order parts.