3D printing is the quick, cost-effective, single-step solution for manufacturing any product from a virtual 3D (CAD) model to a tangible production part or a prototype. Even very complex designs can be achieved easily by using 3D printing compared to the conventional machining processes. This article discusses how to choose the most cost-effective 3D printing technology and materials among the options available at Xometry.
Factors affecting the price of 3D printing
Before choosing the most affordable options, it is important to understand the factors that affect the price of 3D printing such as design, material, finishing, quantity, and lead time. Here is the detailed description.
Design
Designing the 3D model of the part is the most important factor that influences the cost. The following factors need to be taken into account as far as costs according to design are concerned.
Geometry
Defining the size of the object is an important factor in influencing the cost of printing. The cost of printing is proportional to the size of the object. The larger the object, the more input print material is required, which in turn increases the cost. Voluminous objects also lead to longer printing cycles and an increase in the cost of printing. Since 3D printing price is proportional to the volume occupied by the object in the machine’s tray, changing a few aspects of the object to make it compact without needing to change the scale of the whole object can reduce the overall price of the object.
Wall thickness
The strength of the object depends on the thickness of the walls but in order to save money, check if some parts can be made thinner. However, walls cannot be too thin: e.g. for FDM the minimum recommended thickness is 1.2 mm; for SLS: 0.7 mm. Different materials have different wall thickness requirements based on the 3D printing process and the mechanical properties. Thinner walls decrease the build time and lower the costs while it could also mean delicate features, gaps and missing pieces. The main considerations should be geometry and part application while choosing the wall thickness.
Hollowing out
Hollowing a part out is indeed a very good way to save material. Less material means a clear reduction of the cost. It is also an effective method to reduce the weight of the part. However, it can slightly affect the overall part strength. It is purely the designer’s decision which areas can be hollow and which areas need to be solid depending on the application.
Layer Height
A 3D printer usually prints the part layer-by-layer. Layer height is the measure of a single layer. If the layer height is more, inherent ridges or “stair-stepping” on the surface of the 3D printed are seen which results in a less smooth surface. Lesser the layer height provides for improved surface quality (high definition) but results in increased price because of the overall build time, as the layers are small and the time taken to build the full part is increased.
Support Structures
3D printing support structures are not part of the model but are used to support parts of the model during printing. Once printing is over, there is an additional task of removing the structures before the model is ready to go. In a production setting, added work means added cost to the model. The amount of support material on your design can also affect the price as it increases the quantity of the material required. For example, In FDM process, support structures are required, whereas, in SLS and MJF, they are not required. Optimizing the design with self-supporting angles (usually around 45 degrees or more) uses less support material and can help reduce material expenses.
Learn more about designing for different 3D printing technologies:
Material
The type of material used to build the part plays a major role in cost determination. If you’re looking for the most affordable material, a simple prototyping photopolymer like Polyamide (PA) or epoxies would be the best fit; if you have more functional requirements like high strength, fine surface finish or heat resistance, the process could get much more expensive.
For example, resins like heat-resisting Polycarbonate, used in the process of stereolithography (SLA) provide heat and corrosion resistance and are also expensive. Materials like Polyamide (PA), used in HP Multi Jet Fusion and fused deposition modeling are very resistant, light and adaptable to a wide range of applications and are much cheaper. It is important to know beforehand which properties are desired in order to get the price cheaper.
Finishing options
After printing, based on how sophisticated the part is meant to be, different post-processing works are done. For example, the raw texture of the print may not have an aspect that suits the application. In that case, extra polishing work is required to get rid of the imperfections of the product. These processes are common for thermoplastics and some resins. Removal of support structures and customizing the 3D prints with different colours is also a common post-processing work.
Since not all printing technologies are able to add colours to the material while printing, dyeing or painting (expensive) is meant to be done. The list of all extra finishing works needed goes on with respect to the application, for instance, varnishing or shot-peening works (used for metals). These post-processes require additional labour, machine time and hence increase the price.
Quantity
One of the options to reduce 3D printing costs is considering 3D printing as a production technique and an alternative to conventional processes. For example, bulk production of 20 units of the same part will have a significant effect on the price compared to a single part. It provides an adapted cost that can be reduced by up to 80% compared to the initial unit cost.
Lead time
Lead time plays a big role in the cost of a part. If the part needs to be manufactured immediately, extra work time and faster delivery will reflect in the final price.
Affordable 3D printing technologies available at Xometry
If you’re looking to produce affordable 3D prints, you should consider one of the three technologies: Fused deposition modelling, selective laser sintering or HP Multi Jet Fusion. All these technologies provide great quality for an affordable price.
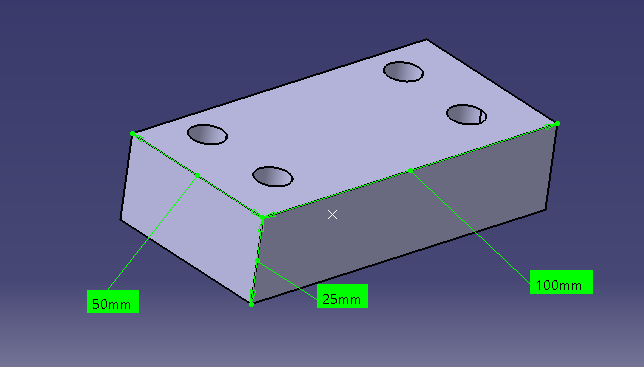
Let’s take this model as a reference and compare these 3 technologies.
Fused Deposition Modeling (FDM)
FDM is one of the popular and affordable technologies. In this process, a product is built by selectively depositing melted material in a pre-determined path layer-by-layer. The materials used are thermoplastic polymers and come in a filament (thin wire-like) form.
Materials: Thermoplastic filaments (ABS, Nylon, Polycarbonate, PEEK, etc.)
Pros:
- Large Part sizes can be achieved and very less post-processing
- Wide variety of Selection and colors available
- Quick
- Cheap compared to other processes
Cons:
- Marks after removing support material
- Misses small details
- Non-Smooth or Layered finish
Consider that the reference model has to be printed in FDM and we take examples of two thermoplastics used, ABS and ULTEM 9085 HP TP, while ABS being the cheaper and widely used material whereas ULTEM 9085 HP TP is a material with high mechanical properties and used rarely.
Material | Cost if a single unit is ordered | Unit cost if 20 pieces are ordered |
ABS | 22.18€ | 22.15€ |
ULTEM 9085 HP TP | 106.1€ | 93.02€ |
According to the above table, in both cases, the production of the parts in bulk quantities result in lowering the overall final price. These are the prices for the standard delivery, whereas express delivery is much more expensive.
Selective Laser Sintering (SLS)
Selective laser sintering (SLS) is one of the most popular 3D printing technologies which produces highly accurate and durable parts that are perfect for end-use, low-to-mid volume production, or rapid prototyping. Though SLS provides high detail quality and perfect production repeatability, it is one of the cheapest options for industrial 3D printing services because it can build parts in bulk without support structure requirements.
Materials: Thermoplastic powders (e.g. PA 12, TP)
Pros:
- Cheap
- Design freedom
- Durable, versatile, flexible and Corrosion resistance (Nylon)
- Scalable and Fast
Cons:
- Surface Roughness
- Warping and Creep issues in large features
- Less choice of colors
Consider that the reference model has to be printed in SLS and we take examples of two thermoplastics used, Nylon PA 12 and Flex TPU M95A PU and their cost comparisons.
Material | Cost if a single unit is ordered | Unit cost if 20 pieces are ordered |
Nylon PA 12 | 79.72€ | 57.77€ |
Flex TPU M95A PU | 121.76€ | 109.86€ |
Multi Jet Fusion (MJF)
HP Multi Jet Fusion is a powerful and affordable 3D printing technology that produces highly accurate and durable parts at fast speeds, especially compared to other technologies. Multi Jet Fusion parts are great for end-use, low-to-mid volume production, rapid prototyping, or as a bridge process to injection moulding.
Materials: Thermoplastic powders (e.g. PA 11, PA 12, or TPU)
Pros:
- Freedom of design since no support is required
- Cheap for a small series
- Durable, Versatile, flexible and Corrosion resistance (Nylon)
- Scalable and Fast
Cons:
- Surface Roughness
- Limited Post processing options
- Warping and Creep issues in large features
- Less choice of colors
Consider that the reference model has to be printed in MJF and we take examples of two thermoplastics used, Nylon PA 12 and TPU PU 88/95A and their cost comparisons.
Material | Cost if a single unit is ordered | Unit cost if 20 pieces are ordered |
Nylon PA 12 | 18.29€ | 15.96€ |
TPU PU 88/95A | 21.81€ | 16.62€ |
The materials in the above table are cheaper and widely used. They also exhibit the same properties apart from colour and are hence cheaper in price.
Conclusion
The three processes, FDM, MJF and SLS, use almost the same thermoplastics which are comparatively cheap and widely used. Thermoplastics, like PA or ABS, can be a good fit for prototyping and modelling applications, yet the quality and the details they offer are low.
In our comparison, the cheapest option for the model we used was MJF 3D printing in combination with PA12, but we recommend to always check all three technologies and the available materials. Get your instant quotes in the Xometry Instant Quoting Engine.